How to Reduce Delivery Lead Times: Key Strategies for Faster Shipping
A report by CNBC estimates that around 20% of small businesses fail within the first year. This can occur due to a variety of reasons, but a consistently poor customer experience is one of the most common.
Faster delivery can mean the difference between a loyal customer and a lost sale. Delays often come from simple issues that better systems and planning can solve. Businesses that focus on the right shipping solutions often see quicker turnarounds and fewer complaints.
Small changes in workflow and communication can add up fast. Let’s explore the key steps you can take to reduce delivery times.
Streamlining Order Processing
Delays often begin at the start. When orders sit in a queue or require manual checks, time is lost before anything even ships.
Clear workflows and automatic confirmation emails help move things along. Using integrated systems that sync sales with shipping solutions removes extra steps. Every saved minute here speeds up the entire journey.
Improving Inventory Accuracy
Mismatched inventory records cause major slowdowns. A product might show in stock when it’s not, leading to backorders and unhappy customers. Barcode scanning and routine checks help prevent this.
Technology that links inventory with sales channels can flag low stock before it becomes a problem. Mistakes in inventory waste time and break trust.
Choosing the Right Carriers
All shipping partners are not equal. Some specialize in specific regions, while others are more reliable for international freight.
Matching the right carrier to the right job makes a difference in how fast deliveries arrive. When businesses switch blindly between providers, delays and confusion follow.
Smarter planning with fast delivery options in mind brings better results. To make more informed decisions, consider the following:
- Delivery speed by region
- Tracking accuracy
- Cost predictability
- Experience with high-volume routes
- Customer service responsiveness
The right match leads to fewer disruptions and more consistent outcomes.
Upgrading Fulfillment Centers
Old systems in warehouses can slow everything down. When workers rely on outdated software or slow equipment, the whole process suffers.
Updated fulfillment tools give teams better control over sorting and packing. Some businesses even work with third-party centers to expand reach and save time. Investing here improves how fast products move from shelf to shipment.
Reducing Warehouse Downtime
Idle time in a warehouse adds up. When teams wait for instructions or sort through disorganized inventory, nothing gets shipped.
Real-time dashboards and clear task assignments keep things moving. Even something as simple as labeling shelves better can improve speed.
Many effective logistics strategies start with small internal changes like these. To minimize downtime, make use of:
- Clear pick-and-pack workflows
- Regular equipment maintenance
- Shift handoff checklists
- Cross-training for flexibility
- Visual inventory systems
Every adjustment adds speed without sacrificing accuracy.
Planning Smarter Routes
Poor routing decisions slow things down, especially when fuel costs and driver hours are tight. Using route optimization software can help companies avoid traffic and minimize backtracking. Routes that work well one day may not work the next, so frequent adjustments matter.
Companies focused on ecommerce shipping often rely on real-time updates. Getting packages to doorsteps faster takes smart planning on the ground.
Improving Vendor Communication
Vendors often play a more substantial role than expected. Delays upstream affect everything downstream. Strong communication can prevent these issues or reduce their impact.
When vendors know your timelines and expectations, they’re more likely to stay on schedule. Timely updates keep your supply chain management efforts strong and predictable. Build better relationships by focusing on:
- Shared production calendars
- Early alerts for delays
- Collaborative forecasting
- Agreed turnaround times
- Regular check-in calls
Vendor trust speeds things up and reduces the chance of surprises.
Automating Repetitive Tasks
Many delays are caused by tasks that could be automated. Manual label printing or invoice generation takes time away from actual shipping. Using tools that handle these steps frees up staff for higher-value work.
Automation also reduces errors, which helps speed things up in the long run. Freight solutions that include automation features make an even more substantial impact.
Coordinating Better with Partners
Smooth coordination between departments and outside partners often goes overlooked. Everyone in the chain must work from the same information to avoid delays.
Shared dashboards and unified platforms keep all parties aligned. Visibility matters, from purchase order to delivery confirmation. Even one misstep in coordination can add days to a timeline.
Analyzing Delays and Fixing Bottlenecks
Data shows where problems occur. When companies review their performance regularly, they find patterns in missed delivery times or customer complaints.
These insights help fix the specific issues slowing things down. Improvements can happen at packing stations or even in how returns are handled.
Businesses focused on improving shipping solutions must be willing to adjust and evolve. To uncover the true causes of delay, track:
- Average delivery times by region
- Order accuracy rates
- Frequency of returns
- Warehouse processing times
- Communication gaps in the order flow
Fixing small delays often unlocks large gains in speed and reliability.
Finding the Right Logistics Platform
Choosing the right logistics platform can make or break your delivery speed. A strong platform connects every part of your supply chain in one place. It should offer real-time updates and tools to manage both domestic and international shipments.
Look for a platform that supports multiple carriers and provides detailed performance reports. Customization also matters, and flexibility is key.
Avoid platforms that require constant manual input or don’t scale with growth. The right fit will reduce errors and give your team the control they need to meet rising customer expectations.
It should also enhance communication across departments and improve visibility from order to delivery. A solid logistics platform helps you spot issues early, adapt quickly, and maintain consistent service levels.
As demands shift, your platform should evolve with you. Long-term success depends on systems built to grow, not slow you down.
Leverage Premier Shipping Solutions
Reliable shipping solutions bring order to the chaos and help teams meet tight deadlines without cutting corners. Better systems lead to smoother days and stronger customer trust.
ACI Logistix delivers fast, transparent small parcel logistics across the US, supporting both online and offline commerce. With real-time tracking, geo-confirmation, and end-to-end routing tech, we ensure accuracy and speed. You can get in touch with us today to learn more about how we can help.
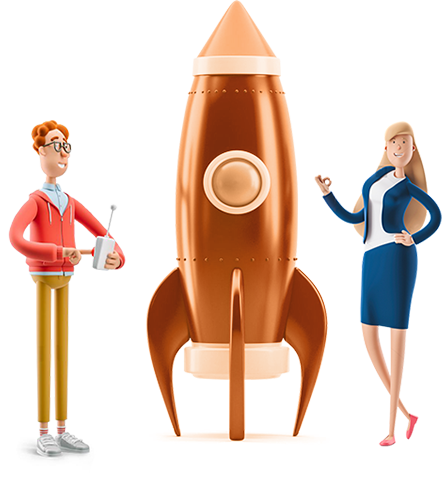
Join our Newsletter
Get all the latest news directly to your inbox!
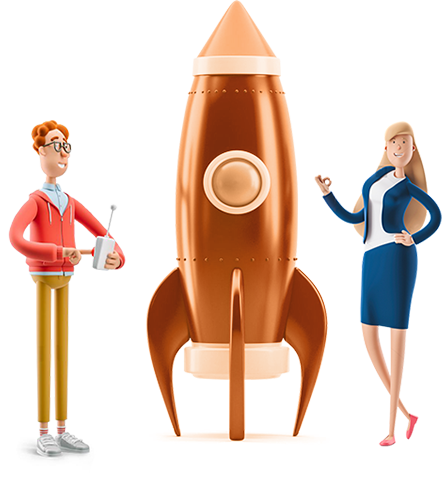
Join our Newsletter
Get all the latest news directly to your inbox!
Related Posts
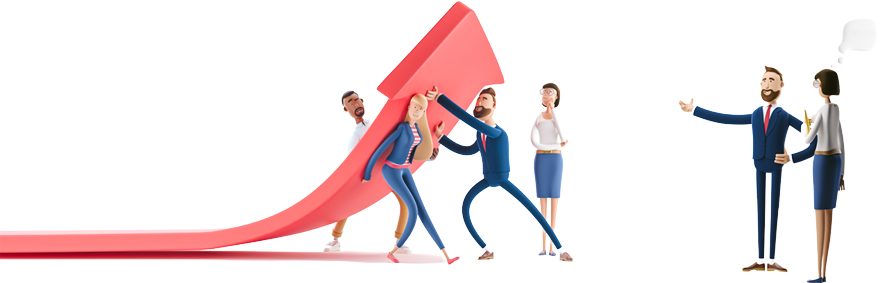